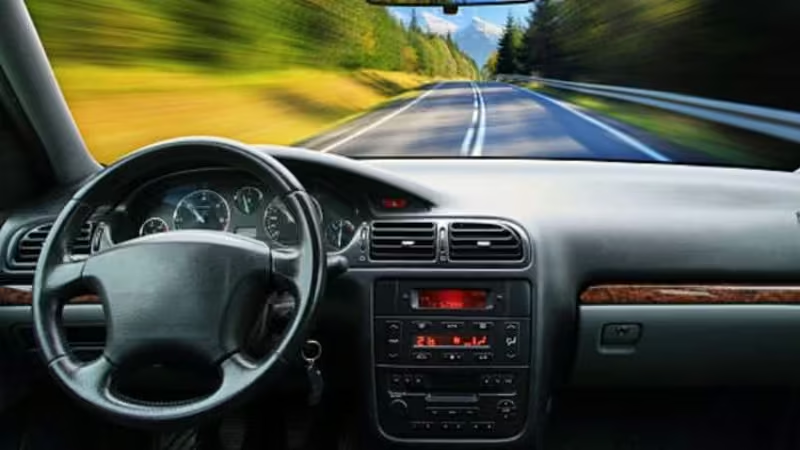
Dashboard Automobile Guide
Dashboard automobile is a critical element in vehicle, serving as the driver’s primary interface with the auto dashboard car system.
Compression molding is a widely used manufacturing process to create a variety of products we use in our daily lives. It’s known for its versatility, cost-efficiency, and ability to produce high-quality parts.
This article will take an in-depth look at compression molding, you will have better understanding of the following topics:
In compression molding, a precisely measured quantity of heated molding material is compressed within a heated mold’s shape, typically composed of upper and lower halves. The mold can comprise multiple components operating as a unified system during compression. Once the mold’s two halves meet, they form a cavity in the desired product’s shape.
Among various molding methods, compression molding was initially devised for synthetic materials, making it the most cost-effective choice for thermosetting materials.
Compression molding is a permanent molding process that is practical and commercially viable. The molds for compression molding can be reused for multiple production cycles.
The key steps involved in the compression molding process are detailed below.
Once the mold is created, it must undergo preparation before production. Typical preparation steps include: cleaning the mold, applying a release agent, heating it up, and performing other necessary setup processes.
Choose the material for your molding process and ensure you use the proper amount. Using excessive material will cause overflow and result in flash, which will need manual removal and result in material wastage. Then place the material on the lower part of the mold to achieve optimal compression results.
Close the upper part of the mold, apply pressure, and wait for your piece to form. Many manufacturers also use heat during the compression process, which softens the raw materials and can help speed up production.
Three important parameters during compression are:
1. Temperature – This influences viscosity. Lower viscosity enhances the flow and consistency of the material. In contrast to deformation:
2. Pressure – The pressure is related to material density. Higher density materials require higher pressure to achieve comparable effect. For example, carbon fiber-reinforced polymers typically require a pressure of 2-14 MPa, depending on the fiber density.
3. Time – Compression can occur gradually, sometimes with a holding period during which the material remains compressed and heated. The compressive force can also be applied and removed rapidly, without necessarily having a sudden impact, as is the case in forging.
Once the material has hardened and taken the shape of the mold, it is ejected, which can be done manually or using automation. Manual ejection is more common in small-scale molding applications. Automated ejection typically involves a plunger that extends from the underside of the mold when ejection is required or uses a separate mechanism with suction cups.
After ejection, the flash remains attached to the product and should be removed, which is called de-flashing.
De-flashing can be a manual or an automated process. Manual de-flashing is typically done where the molded product is exceptionally large and cannot be handled by automated de-flahsing machines. Automated de-flashing typically uses water jets, ice blasting, or vibration tumbling.
There are three types of compression molds, listed as follows:
In the flash-type of compression molding, an excess of charge material is loaded, resulting in the generation of flash at the end of compression.
The flash produced is typically horizontal. If the mold is closed too slowly, it can result in heavy flash formation. On the other hand, closing the mold too quickly can lead to lower density in the molded part and reduced strength.
Positive-type mould is designed to create the exact shape and dimensions of the final product, it requires an accurately measured molding material. The structure of the positive mold is relatively complicated and the manufacturing cost is high. The upper and lower parts of the mold fit together perfectly to define the desired shape of the molded part. The operation technology requirements are high during pressing.
This is in between the other two methods of controlling flash and is the most expensive of the three. However, it combines the advantages of the two different mold types. The material can flash out during pressing but is subject to certain restrictions.
Both thermoplastics and thermosets are compatible with compression molding. They offer a wide range of material options that vary in terms of price and performance. Thermoset materials, on the other hand, include plastics and other polymers that become irreversibly cured when exposed to heat. This means they can only be molded or shaped once. The compression molding process induces a chemical transformation in thermosets that can’t be reversed or repeated. Common compression molding materials are as follows:
Thermoset resins: polyurethane, silicones, phenolic, unsaturated polyesters.
Thermoplastics resins: Polypropylene, Nylon, UHMWPE, HDPE, Acrylics
Elastomers: NBR, SBR, EPDM, FKM, Silicone Rubber
Fiber types: fiberglass, aramid, standard modulus carbon fiber, as well as other grades of carbon fiber.
Choosing compression molding for a rubber or plastic component manufacturing project offers numerous advantages. In addition to the typical benefits of molding parts such as excellent surface finish, versatile design options, and high product uniformity, compression molding provides the following advantages.
It is a low-cost operation and involves lower tooling costs
Compression molding is simpler compared to other manufacturing methods. It requires less infrastructure for tooling, making equipment and tools more straightforward. This typically means lower capital investment. Tools can be made from more cost-effective materials like aluminum or lower-grade steel, reducing costs. However, tools must withstand high molding pressures. The process is labor-intensive, but proper handling results in minimal mold wear, translating to lower maintenance costs and customer quotes.
It is good for large or thicker parts
As the compression molding process directly loads material into the mold cavity, it doesn’t have part weight limitations, except those determined by part design and equipment. As a result, this method is ideal for producing large parts that require a significant bulk of material to manufacture. In injection molding, part weight is constrained by injection barrel capacity.
It is cost-effective for small production runs
Compression molding is the cost-effective choice for small to medium-production runs, including prototyping and sampling before large-scale manufacturing. The lower capital cost for tooling and setup makes it an efficient option for producing smaller runs of parts.
It has no gates, sprues or runners
This form of moulding does not use gates, sprues or runners which are tooling features that materials have to pass through in other methods of production before entering the mould cavity. These can consume extra material and therefore cost and can also detract from the cosmetic requirements of a part.
Although there are many benefits to using compression molding, it does have its limitations, it also has a few disadvantages, such as:
It does not work well for complex parts
The product’s geometry is limited to enable ejection while ensuring the reuse of the mold. Compression molding isn’t the ideal process for manufacturing complex parts such as those with severely slanted angles, undercuts or some small details.
It has a long cycle time that causes slower process times
Because the thermal conductivity of rubber and resins is relatively poor, compression molding usually requires more time to bring the material to a cured state. Depending on the size of a part, a typical cycle can take around ten minutes. These slower processing times can affect production rates and costs in higher-volume projects.
It is difficult to control flash which leads to higher post-molding costs and material waste
During the compression molding process, it is necessary to push air out of the cavity using excess material to create a void-free part, which causes flash and burr issues and again increases material wastage. Even if the part size and weight is carefully calculated, it is inevitable. These have to be manually or mechanically cut off, meanwhile, the waste thermoset rubber or plastic generally cannot be melted down and reused.
Compression molding finds application across a wide range of industries. Below, we’ll explore common examples of products and components that incorporate compression molded parts.
Dashboard automobile is a critical element in vehicle, serving as the driver’s primary interface with the auto dashboard car system.
Plastic molding toys, crafted through the precise process of injection molding, bring vibrant, durable playthings to life. This guide explains
What is Medical Injection Molding? Medical injection molding is a precision manufacturing process that shapes biocompatible plastics into high-quality components
Auto CNC machining crafts intricate components for automotive industry with unmatched accuracy. From engine blocks to custom prototypes, automotive CNC
We give value to the excellence and top class engineers, but in terms of accurate service.
Copyright © 2025 Hebei Zhongren Rubber and Plastic Co., Ltd All rights reserved.
Send Your Inquiry Today!