Rubber molding is a versatile manufacturing process capable of yielding an extensive array of products, ranging from fundamental seals and gaskets to complex automotive components. It is known for its cost-effectiveness and remarkable precision, and it has emerged as a favored choice across diverse industries. There are 3 techniques in the rubber molding processes: injection, compression, and transfer molding. Each method boasts distinct advantages tailored to specific applications. In this post, we will explore each rubber molding technique, and learn the charm of rubber molding
What is Rubber Molding?
Rubber molding is a manufacturing process that transforms uncured rubber or elastomeric materials into usable products. Rubber molding involves placing raw rubber material into a mold cavity, and then applying heat and pressure to cure and shape the rubber into the desired part or product. Rubber molding allows for the production of a wide variety of rubber products including seals, gaskets, grommets, boots, and more. Key advantages include high precision, consistency, complex geometries, and the ability to bond rubber to metal.
The Rubber Molding Process
The rubber molding process typically involves a series of steps:
1. Design and Prototyping:
The process begins with the design of the rubber component. Engineers use computer-aided design (CAD) software to create precise 3D models of the part. Prototyping may also be conducted to test the design and make any necessary adjustments before proceeding to production.
2. Material Selection:
Choose the appropriate rubber material based on the component’s intended application, environmental factors, and performance requirements. Common rubber materials include natural rubber, synthetic rubber (such as silicone or EPDM), and various elastomers.
3. Mold Design and Production:
Once the design is finalized and the material selected, a mold is created to shape the rubber into the desired form. Mold design involves considerations such as part geometry, mold material, and cooling channels. The mold can be made of metal (such as steel or aluminum) or certain polymers, depending on factors like expected production volume and part complexity.
4. Rubber Preparation:
Raw rubber material is mixed with additives, fillers, and curing agents to create a rubber compound with the desired properties. This compound is then prepared for molding by heating and shaping it into a form suitable for injection, compression, or transfer molding.
5. Molding Process:
Injection Molding: Molten rubber material is injected into a mold cavity under high pressure. Once cooled and solidified, the part is ejected from the mold.
Compression Molding: Preheated rubber material is placed into an open mold cavity, which is then closed under pressure. Heat and pressure are applied to the mold to cure the rubber into the desired shape.
Transfer Molding: Similar to compression molding, but the rubber material is preheated in a separate chamber before being forced into the mold cavity under pressure.
6. Curing:
After the rubber material has been molded into the desired shape, it undergoes a curing process to strengthen its molecular structure and improve its physical properties. Curing can be accomplished through heat, chemical reaction, or a combination of both, depending on the rubber compound used.
7. Finishing and Quality Control:
Once cured, the rubber component is removed from the mold, trimmed to remove excess material, and inspected for defects or imperfections. Quality control measures ensure that the finished components meet specified tolerances and performance criteria.
The Different Types of Rubber Molding
As we mentioned before, there are 3 different types of rubber molding:
Compression Molding:
Compression molding is a traditional rubber molding method ideal for producing parts with simple to moderate complexity. In this process, preheated rubber is placed into an open mold cavity, which is then closed under pressure. Heat and pressure cause the rubber to fill the mold and cure, typically through vulcanization. Once cured, the part is removed, trimmed, and inspected for quality.
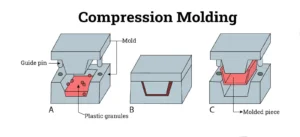
Advantages of Rubber Compression Molding:
- Low Cost: Simple tooling design and reduced production costs with higher volumes.
- Low Maintenance: Easy to clean and repair due to the simple design.
- Material Variety: Handles a wide range of rubber materials without relying on material flow.
- No Gate Vestige: No gate marks on the final product, improving aesthetics and reducing finishing costs.
Disadvantages of Rubber Compression Molding:
- Dimensional Tolerance: Less precise than injection molding, with potential deviations in complex shapes.
- Finishing: Requires additional work to remove flashes and parting lines, adding time and cost.
Applications of Rubber Compression Molding:
- Seals & Gaskets: Used in door/window seals, gaskets, O-rings, and stoppers.
- Shock Absorbers & Protective Parts: Vibration dampers, protective covers, and cable sleeves.
- Consumer & Medical Products: Rubber mats, appliance seals, and medical stoppers.
Transfer Molding:
Transfer molding combines elements of injection and compression molding. Preheated rubber is placed into a chamber (the pot) next to the mold cavity. A plunger forces the rubber into the mold through a runner system and gate. Heat and pressure cure the rubber, and once completed, the molded part is removed, trimmed, and inspected.
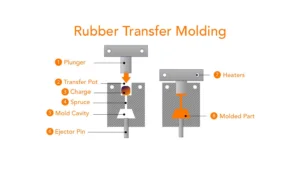
Advantages of Rubber Transfer Molding:
- Tight Tolerance: Provides accurate part geometries with high dimensional precision.
- Metal Bonding: Ideal for manufacturing rubber-to-metal bonded parts, like metal-rubber mounts.
- Large Parts: Can easily accommodate large mold cavities.
- High Cavity Count: Simple preforms are reusable for many cycles, saving time and effort.
Disadvantages of Rubber Transfer Molding:
- High Tooling Cost: Mold complexity increases the initial setup cost due to features like the pot and sprue.
- Finishing: Requires deflashing to remove excess material.
- High Cycle Time: Longer curing time compared to other processes, affecting production speed.
Applications of Rubber Transfer Molding:
- Sealing Components: Gaskets, O-rings, and seals used in automotive, industrial, and electronic applications.
- Electrical & Electronic Parts: Insulators, connectors, and protective covers for electronic devices and wiring.
- Medical Devices: Rubber parts such as stoppers, seals, and diaphragms used in medical equipment.
- Custom Rubber Parts: Engineered components like bushings, dampers, and vibration isolators for specialized uses.
Injection Molding:
Rubber Injection molding is a highly versatile and precise process used to manufacture rubber components, from small, intricate parts to larger, complex shapes. In rubber mold injection, raw rubber is heated to a molten state and injected into a closed mold under high pressure. This forces the rubber to flow into the mold’s details, creating an accurate replica of the part’s shape. Once cooled and solidified, the part is ejected, trimmed, and inspected.
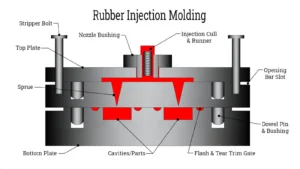
Advantages of Rubber Injection Molding process:
- High Accuracy: Pressurized injection ensures precise filling of the mold, even in intricate details.
- High Mechanical Strength: Parts have strong durability due to ample pressure and curing time.
- No Finishing Required: Minimal defects or excess material, only small parting lines or gate vestiges.
- Quick Process: Optimized control of heat and pressure leads to short curing cycles and faster production.
Disadvantages of Rubber Injection Molding process:
- Material Limitations: Requires flexible, liquid-like rubbers (e.g., silicone, polyurethane), limiting material options.
- High Initial Costs: Expensive tooling and machinery make it less viable for low-volume production.
Applications of Rubber Injection Molding:
- Seals & Gaskets: O-rings, gaskets, and seals.
- Electronic Components: Connectors, insulators, and waterproof parts.
- Medical Parts: Stoppers, seals, and valves.
- Consumer Products: Grips, handles, and protective covers.
How to Choose the Right Rubber?
Choosing the right rubber for your application involves considering several key factors:
1. Temperature Resistance: Identify the temperature extremes your product will face. For high temperatures, use heat-resistant compounds like Silicone. For colder environments, choose rubbers that remain flexible in freezing conditions.
2. Environmental Stress: Assess exposure to factors like UV rays, chemicals, or moisture. Weather-resistant rubbers are ideal for outdoor use, while chemical-resistant options are necessary for industrial settings.
3. Physical Forces: Consider the mechanical stresses your product will endure, such as tension, compression, or impact. High-tensile materials like Natural Rubber or Neoprene are suited for demanding applications.
4. Budget: Balance cost and quality. While materials like EPDM are more affordable, they may require more frequent replacements compared to more durable options like Silicone. Choose based on the longevity and performance needed.
Rubber Materials Options for Rubber Molding
Rubber molding offers a wide range of material options, each with its own unique properties and suitability for specific applications. Here are some common rubber materials used in rubber molding:
Natural Rubber (NR):It offers excellent elasticity, resilience, and tear resistance, making it suitable for applications requiring high flexibility and durability. It is commonly used in products such as seals, gaskets, tires, and conveyor belts.
Styrene Butadiene Rubber (SBR): Offers good abrasion resistance and flexibility, commonly used in automotive and industrial applications.
Nitrile Butadiene Rubber (NBR): Known for its oil and fuel resistance, suitable for sealing applications in automotive and aerospace industries.
Ethylene Propylene Diene Monomer (EPDM): Exhibits excellent weathering, ozone, and UV resistance, commonly used in outdoor applications and automotive seals.
Chloroprene Rubber (CR): Offers good weather resistance and flame retardancy, used in gaskets, hoses, and industrial applications.
Polyisoprene Rubber (IR) : Produced through the polymerization of synthetic isoprene. Exhibits high tensile strength, tear resistance, and resilience. Suitable for applications requiring a high-purity, resilient rubber material.
Neoprene (CR): A fire-resistant rubber with strong abrasion properties. Used in applications like motor components, shock absorbers, and seals.
Silicone Rubber (MVQ): It offers exceptional heat resistance, flexibility over a wide temperature range, and resistance to aging and weathering. It is commonly used in medical devices, automotive seals, electronics, and kitchenware.
Fluoroelastomers (FKM): Fluoroelastomers, such as Viton®, are highly resistant to heat, chemicals, and oils. They are commonly used in applications requiring exceptional chemical resistance, such as seals and gaskets in the automotive, aerospace, and chemical processing industries.
Fluorosilicone Rubber (FSR): Combines the temperature resistance of silicone with added resistance to oils, fuels, and solvents. Suitable for aerospace and other applications requiring chemical resistance.
Polyurethane (PU): It offers a balance of elasticity, abrasion resistance, and chemical resistance. It is often used in applications such as wheels, rollers, seals, and bushings in industrial and automotive settings.
Get Our More Material Options
Products of Rubber Molding
Rubber molded parts are essential for sealing, vibration dampening, and shock absorption. Here are common types:
Rubber O-Rings: Circular seals used to prevent leaks in hydraulic, pneumatic, and automotive systems. They ensure tight seals under pressure.
Rubber Seals: Flexible seals in various shapes (rectangular, circular, square) to prevent leakage of fluids and gases, used in automotive, aerospace, and industrial applications.
Rubber Gaskets: Thin, flat seals for preventing leaks in pumps, compressors, engines, and industrial pipe connections.
Rubber Tubing: Flexible tubing for fluid transfer in medical devices, factories, and chemical processing.
Rubber Bumpers: Impact-absorbing components to protect surfaces from scratches and damage in automotive, electronics, and furniture.
Rubber Bushings: Cylindrical components that reduce friction and wear in automotive suspension systems and machinery.
Rubber Diaphragms: Flexible sealing elements that manage fluid flow in pumps, valves, and medical equipment.
Rubber Grommets: Protect wires and cables from abrasion and sharp edges in automotive and electrical applications.
Rubber Isolators: Vibration isolation components used in machinery, HVAC systems, and electronic equipment.
Rubber Suction Cups: Create vacuum seals for material handling, packaging, and robotics.
Rubber Washers: Precision discs used for load distribution, sealing, and vibration control in plumbing, automotive, and industrial systems.
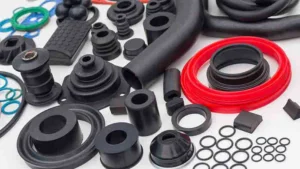
Industries Application of Rubber Molding
Rubber-molded products are essential across a wide range of industries due to their durability, flexibility, and resilience. Key industries include:
- Aerospace: Rubber parts like seals and vibration dampeners ensure safety and performance under extreme temperatures and pressures, meeting high standards for flight systems.
- Automotive: Rubber components, including seals, gaskets, and mounts, enhance vehicle durability, safety, and performance, with added noise suppression and resistance to chemicals and temperature extremes.
- Printing: Rubber rollers, pads, and mountings are crucial in ink transfer, shock absorption, and vibration reduction, ensuring efficient and high-quality printing operations.
- Home Appliances: Rubber seals, gaskets, and non-slip components improve appliance longevity, safety, noise reduction, and user ergonomics by preventing contamination and electrical hazards.
- Electrical: Rubber products like outlet covers and seals protect against electrical hazards, moisture, and electromagnetic interference, ensuring safety and compliance with industry standards.
- Agriculture: Rubber gaskets and seals protect agricultural equipment from leaks, harsh weather, and chemical exposure, ensuring safe handling of fertilizers and pesticides.
- Medicine: Rubber seals, gaskets, and tubing are integral to medical equipment, offering durability, recyclability, and adherence to stringent health and safety standards.
- Food and Beverage: Rubber products used in this sector must be FDA-compliant, non-toxic, and resistant to cleaning processes, ensuring hygiene and safety in food processing.
- Chemical: Rubber’s resistance to harsh chemicals and extreme temperatures makes it ideal for seals, gaskets, and custom components in chemical processing, ensuring secure and leak-free operations.
Conclusion
In conclusion, rubber molding stands as a cornerstone of modern manufacturing, offering a versatile and cost-effective means of producing a diverse array of components for various industries.
The best rubber molding method and material depend on the application, but experience and creativity are key. At a professional rubber molding company, we combine expertise and design sensibility to create top-quality custom rubber parts.