The use of automotive plastic material is not just a trend but a strategic choice. It can meed the requirements for lighter, safer, and more efficient vehicles. From plastic parts in automobiles like bumpers and dashboards to intricate automotive plastic fasteners and automotive plastic adhesives, these materials are versatility. This article explores why automotive plastic is indispensable, details the examples of plastic materials used, highlights selection considerations, and underscores why choosing the right plastic material used in the automotive industry is critical for performance and safety.
Why Are Plastics Used in the Automotive Industry?
The automotive industry faces increasing pressure to improve fuel efficiency, reduce emissions, and enhance vehicle safety and comfort. Plastics in automobiles offer a solution to these challenges.
One of the primary reasons plastics are used in cars is their lightweight nature. Plastic parts in automobile manufacturing can significantly reduce vehicle weight compared to traditional metal components. For example, replacing metal with polypropylene or polyethylene can lower the overall weight of a vehicle, leading to better fuel economy and extended electric vehicle range. Studies show that a 10% reduction in vehicle weight can improve fuel efficiency by 6% to 8%.
Beyond weight savings, plastics resist corrosion and chemical damage far better than metals. This resistance extends the lifespan of automotive plastic fasteners, adhesives, and other components, especially in harsh environments exposed to moisture and chemicals.
Plastics also offer design flexibility, allowing manufacturers to mold complex shapes and integrate multiple functions into single parts, which is difficult or costly with metals. Additionally, plastics contribute to improved safety by absorbing impact energy in collisions, thus protecting passengers. At Zhongren, we provide automotive plastic molding services that meet both safety and performance requirements.
Types of Automotive Plastic Materials and Their Applications
A variety of plastic materials used in the automotive industry cater to diverse applications, from exterior panels to under-hood components. Below are key examples of plastic materials for automotive, their properties, and their roles in plastic parts in automobiles.
Polyethylene (PE): Flexible and impact-resistant. The chemical stability is perfect. PE is used in plastic auto components like fuel tanks and interior liners.
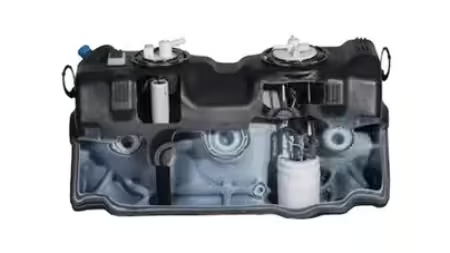
Polymethyl Methacrylate (PMMA): Known for transparency and scratch resistance, PMMA is used in plastics in automobiles for taillight covers and instrument panels.
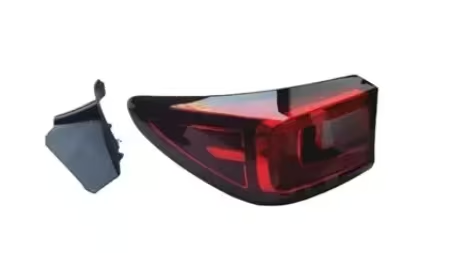
Polypropylene (PP): One of the most common plastics in cars, polypropylene is known for its hardness, durability, and chemical resistance. It is widely used in bumpers, interior panels, cable insulation, and carpet fibers. Its versatility and cost-effectiveness make it a staple plastic material used in the automotive industry.
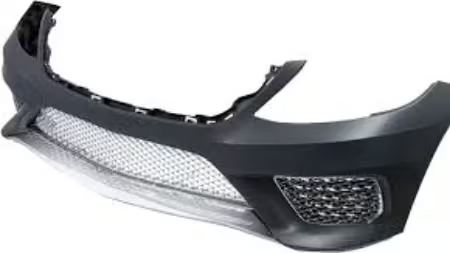
Polycarbonate (PC): With exceptional impact resistance and optical clarity, PC is a go-to material for plastic parts in automobiles like headlamp lenses and windows. Its ability to endure harsh weather conditions, such as UV exposure and extreme temperatures, ensures long-lasting performance. Tesla’s Model S, for example, employs PC headlamp lenses for both safety and aesthetic clarity.
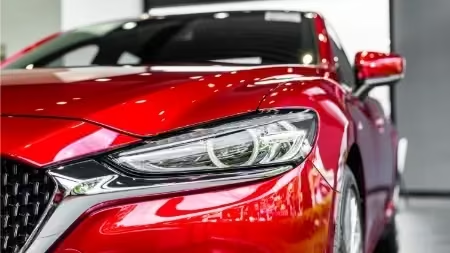
Acrylonitrile Butadiene Styrene (ABS): ABS combines toughness with UV resistance, making it suitable for plastic auto components like dashboards, wheel covers, and door panels. Its machinability allows for precise detailing in interior trims, as seen in Ford’s F-150 dashboard designs, where ABS ensures durability and a polished finish.
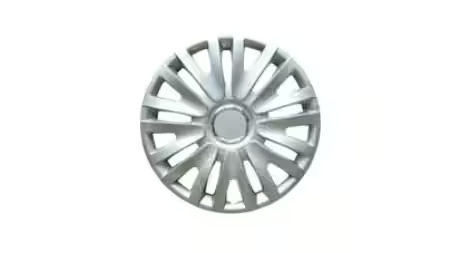
Polyurethane (PU): Available in both soft and hard forms, polyurethane is resistant to solvents and environmental wear. It is flexible and cushioning and used in tires, suspension components, seating, and foam insulation for thermal and acoustic purposes.
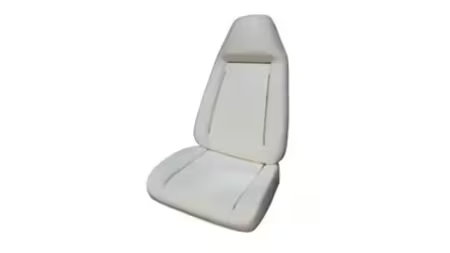
Nylon (Polyamide, PA): Renowned for heat and oil resistance, nylon is critical for plastic auto components in under-hood applications, such as engine covers, fuel system parts, and gears.
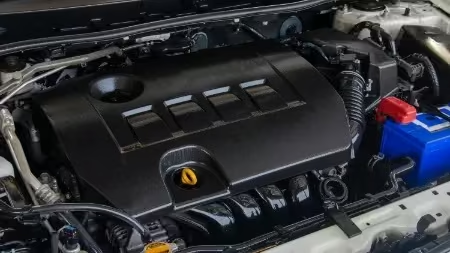
Polyvinyl Chloride (PVC): Making up about 16% of plastics in modern vehicles, PVC offers flexibility, heat resistance, flame-retardant and cost-effective. It can be formulated in soft or rigid forms. It is commonly found in dashboards, automotive body parts, and interior trim.
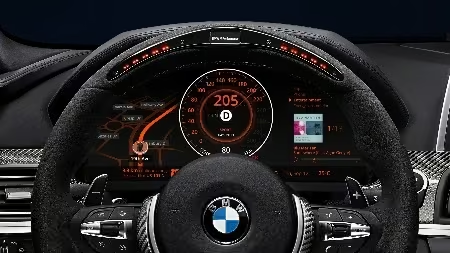
Polyoxymethylene (POM): Known for its low friction and high stiffness, POM is ideal for precision plastic parts in automobiles like gears, bearings, and fuel system components. Its durability under repeated stress suits high-performance vehicles.
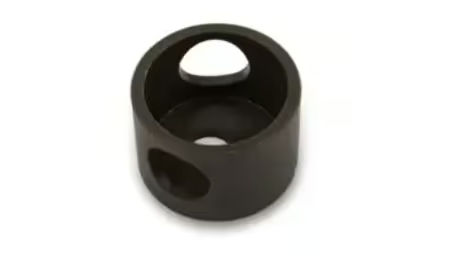
Thermoplastic Elastomers (TPE): These rubber-like plastics are used for seals, gaskets, and flexible automotive plastic fasteners, providing elasticity and durability.
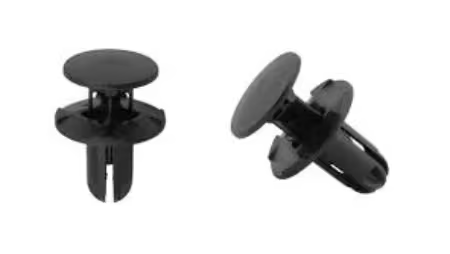
Emerging Materials: Bioplastics, such as bio-based polypropylene and polylactic acid (PLA), are gaining traction in plastics in cars for their eco-friendly properties. These materials, used in interior trims and non-critical components, align with the industry’s push for sustainability.
Considerations for Selecting Automotive Plastic Materials
Choosing the right plastic material used in the automotive industry involves a careful balance of performance, cost, and compliance. Several factors guide this decision:
- Mechanical Properties: Understand the specific functional needs of the part, including mechanical strength, impact resistance, flexibility, and temperature tolerance.
- Environmental Resistance: Evaluate resistance to UV radiation, heat, chemicals, moisture, and weathering to ensure longevity under harsh conditions.
- Cost and Availability: Consider both upfront material costs and lifecycle expenses, including recyclability and environmental impact.
- Manufacturability: Compatibility with manufacturing processes Stufe (Weiter) processes like injection molding is crucial.
- Regulatory Compliance: Compliance with automotive industry standards and safety regulations is essential.
- Weight Considerations: Lightweight plastics reduce overall vehicle weight, improving fuel efficiency and lowering emissions.
- Aesthetic and Surface Finish: The material should support the desired appearance, including colorability, texture, and gloss.
Why Choosing the Right Material is Critical for Automotive Parts
The correct material selection not only effectively enhances vehicle fuel efficiency and reduces emissions but also ensures the durability and reliability of parts under mechanical stress and environmental exposure. Additionally, it improves impact energy absorption to protect occupants during collisions. Proper materials also optimize manufacturing processes, minimize waste, reduce production costs, and support environmental and sustainability goals, such as the use of bioplastics and recyclable polymers.
With extensive industry experience and professional expertise, Zhongren can tailor the most suitable plastic molding material solutions based on your specific needs, considering multiple factors such as the part’s operating environment, mechanical properties, thermal performance, chemical stability, and dimensional stability.
FAQ
How to choose the right plastic for automotive application?
What is the best manufacturing method for automotive plastic materials?
Injection molding is the most common due to precision and efficiency. Other methods like extrusion or thermoforming are chosen based on part shape and volume.