Auto CNC machining crafts intricate components for automotive industry with unmatched accuracy. From engine blocks to custom prototypes, automotive CNC has revolutionized the performance, safety, and aesthetics of automotive components. In this article, we will learn how auto CNC machining change the automotive industry.
What Is Automotive CNC Machining?
Automotive CNC machining refers to the use of computer numerical control (CNC) technology to automate the manufacturing of automotive components. CNC machines operate by following pre-programmed computer software instructions to control machine tools such as mills, lathes, and routers. This process allows for the precise cutting, drilling, and shaping of metal and plastic materials into intricate automotive parts.
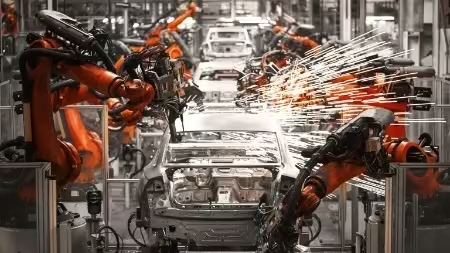
Advantages and Disadvantages of Automotive CNC Machining
The adoption of automotive CNC machining brings numerous benefits but also presents certain challenges.
Advantages
- High Precision and Accuracy: CNC machines follow computer-generated instructions with extreme accuracy, producing parts with tight tolerances essential for automotive safety and performance. The tolerances as tight as ±0.001 inches.
- Increased Efficiency and Productivity: CNC machines reduce production time by automating repetitive tasks, minimizing human error, and boosting throughput for high-volume runs.
- Consistency and Repeatability: Once programmed, CNC machines can produce identical parts repeatedly without variation, ensuring uniform quality across large production runs.
- Design Flexibility: CNC machining supports complex geometries and intricate designs that are difficult or impossible with traditional methods.
- Material Versatility: Automotive CNC machining can process a wide range of materials, including metals like aluminum, steel, and titanium, as well as plastics such as ABS and nylon.
- Customization for Prototyping: Automotive CNC machining excels in creating prototypes and small-batch parts, allowing manufacturers to test designs before committing to full-scale production.
Disadvantages
- High Initial Investment: CNC machines and their maintenance require significant capital expenditure, which can be a barrier for smaller manufacturers.
- Technical Skill Requirements: Operating and programming CNC equipment demands specialized training and expertise.
- Material Waste: As a subtractive manufacturing process, CNC machining generates chips and scrap.
- Size Constraints: CNC machines are less suited for oversized parts, such as large chassis components, due to machine bed limitations.
Applications of Automotive CNC Machining
Auto CNC machining versatility spans from structural engine parts to aesthetic interior features, supporting both standard production and custom manufacturing. For a clearer understanding, explore some practical CNC machining examples that showcase real-world applications in engine, transmission, and interior component manufacturing.
Engine Components: CNC machining is extensively used to manufacture critical engine parts such as cylinder heads, engine blocks, pistons, and crankshafts.
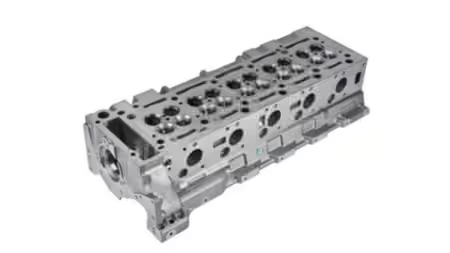
Transmission Systems: Gears, clutch components, and shafts demand exact tolerances for smooth power delivery.
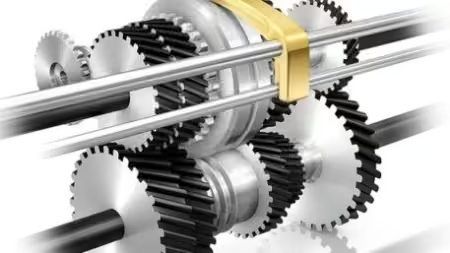
Suspension and Steering Parts: Control arms, ball joints, steering knuckles, shock absorber mounts,and wheel hubs.
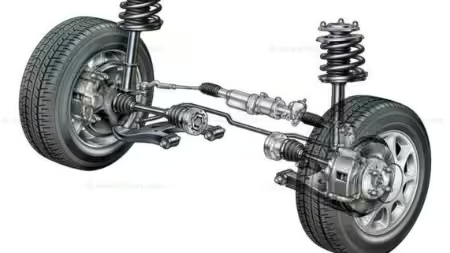
Braking Systems: Brake discs, rotors, master cylinders, and calipers.
Exhaust and Emission Components: Exhaust manifolds, headers, catalytic converters, and mufflers.
Interior and Exterior Components: Dashboard panels, door handles, trim pieces, and lighting housings.
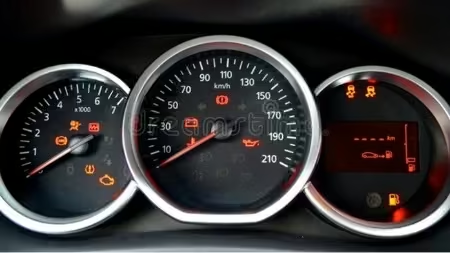
Electrical and Sensor Housings: Connectors, sensor enclosures, and instrument clusters.
Materials Used in Automotive CNC Machining
The choice of material in automotive CNC machining need to balance factors such as strength, weight, corrosion resistance, and cost. Below are the primary materials used and their characteristics.
Aluminum Alloys
Aluminum is prized for its light weight, corrosion resistance, and excellent machinability. It is widely used for engine blocks, cylinder heads, and body structural components. Its thermal conductivity also aids in heat dissipation in engine parts.
Steel
Steel offers superior strength and durability, making it ideal for transmission components, suspension parts, and brake system elements. Various grades, including stainless and alloy steels, provide options for wear resistance and toughness.
Titanium
Titanium combines high strength with low weight and corrosion resistance, making it suitable for high-performance automotive applications such as racing car components.
Cast Iron
Cast iron is a durable, wear-resistant material frequently used in automotive CNC for engine blocks and brake discs. Its high machinability allows for precise shaping.
Copper and Brass
Copper and brass are used primarily for electrical connectors and components requiring excellent conductivity and corrosion resistance.
Plastics (ABS, Nylon, Polycarbonate)
Plastics are common in interior panels, instrument clusters, and non-structural parts. They offer design flexibility, reduced weight, and cost-effectiveness while maintaining adequate strength for their applications.
Outstanding Custom Automotive CNC Machining Service at ZHONGREN
Zhongren state-of-the-art facilities and multi-axis CNC machines deliver high-precision parts tailored to your exact specifications. Our custom CNC machining service includs design consultation, material selection guidance, advanced CNC machining, and post-processing treatments such as polishing, anodizing, and coating, all backed by rigorous quality control to ensure each part meets your exact standards. No matter prototype development or large-scale production.